Key takeaways from this article:
- Why CFD simulations are valuable in marine engineering
- How to set up CFD simulations to achieve reliable results
- How to leverage simulation to improve decision-making, ensuring vessel safety, efficiency, and sustainability
Simulation transforms marine engineering by revolutionizing how vessels and maritime infrastructure are designed, tested, and optimized. For you as a manager, understanding the value of CFD (Computational Fluid Dynamics) is key to unlocking tangible benefits like cost reduction, increased efficiency, and higher quality in projects.
This article is tailored to help leaders grasp the essentials of marine simulation and its strategic importance, whether or not they have a deep technical background. It’s not just a technical tool; simulation is a business-critical decision-making resource. Whether you’re introducing simulation or refining existing workflows, this article will provide a clear overview of how a tool like Fidelity Fine Marine can enhance your projects.
Fidelity CFD, including Fidelity Fine Marine, goes beyond traditional engineering practices by offering managers a powerful platform for forecasting outcomes, managing risks, and aligning engineering decisions with business goals.
It provides a bridge between theoretical design and real-world performance. CFD simulations offer a low-risk environment to test vessel performance under various conditions, helping you evaluate designs, optimize processes, and predict results confidently. This strategic approach minimizes uncertainty and supports long-term success in marine engineering projects.
If you’re interested in delving into the technicalities or aiming to bridge the gap between management and engineering, gaining a deeper understanding of the subject can benefit you.
We’ve made a corresponding guide for engineers: Simulating Marine Engineering: An Engineer’s Guide. This guide highlights the technical complexities marine engineers must navigate to simulate marine phenomena utilizing Cadence’s advanced Fidelity computational fluid dynamics (CFD) software. Whether your goal is to enhance dialogue with technical teams or improve your expertise, this guide is a great place to start.
Fundamental Concepts of Marine Engineering
To set the stage, let’s cover the basics of marine engineering.
Marine engineering focuses on the design, development, operation, and maintenance of systems and equipment used in the marine industry. This includes everything from large cargo ships and offshore platforms to submarines and smaller vessels. Each plays a crucial role in global transport, energy production, and leisure industries.
A key tool in modern marine engineering is CFD (Computational Fluid Dynamics), which simulates how water interacts with vessels and marine structures. CFD helps engineers analyze fluid flows, such as the interaction between waves and a ship’s hull—the main body of a vessel (Figure 1). It is closely tied to hydrodynamics, the study of water movement and its impact on marine components like hulls and propulsion systems.
Key Factors for Vessel Optimization:
- Wave and current interactions – How natural forces affect stability and performance
- Buoyancy and resistance – Crucial for vessel stability and fuel efficiency
- Water flow around hulls – Impacts speed, maneuverability, and safety
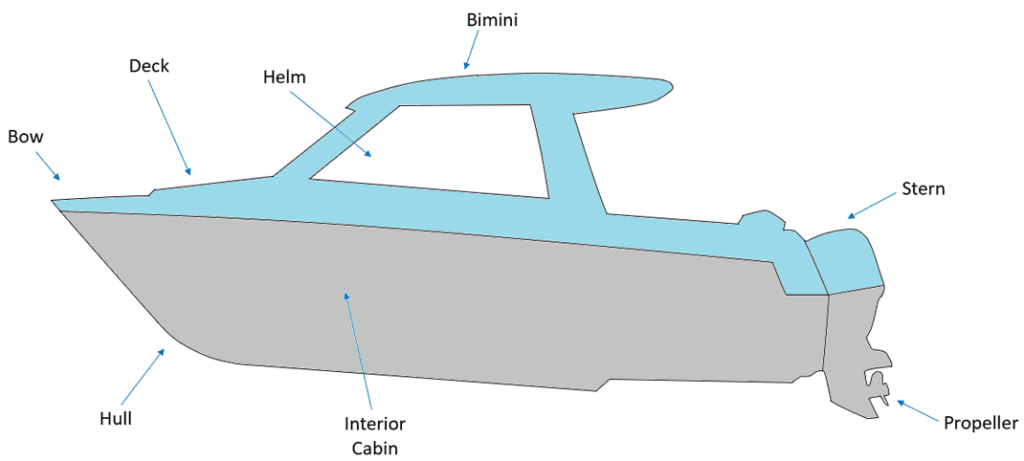
The hull design directly affects a vessel’s performance, stability, and fuel consumption. Each vessel type has a specific hull shape and size, customized for its intended function and operating conditions. Equally important is the propulsion system, which moves the vessel through water. While diesel engines are a traditional choice, gas turbines and hybrid systems are increasingly popular due to their efficiency and lower emissions. Selecting the right propulsion system depends on factors like vessel size, travel distance, and operating costs.
Why Should Managers Understand These Concepts?
As a manager, you don’t need to master the technical details but must grasp the core principles of marine engineering. This knowledge helps in making informed decisions, collaborating effectively with engineering teams, and ensuring projects remain innovative, cost-effective, and compliant with industry regulations. Understanding these fundamentals is essential for overseeing successful marine projects that meet both operational and business goals.
Strategic Importance of Simulation in Marine Engineering
A tool like Fidelity Fine Marine can be a game-changer for long-term strategic planning. Its predictive capabilities allow you to adapt to changing market conditions and evolving regulations, helping you craft resilient, data-driven strategies.
By testing multiple scenarios and predicting potential outcomes, you gain crucial insights that support decision-making on fleet composition, new technology investments, and operational improvements.
Key Benefits of Fidelity Fine Marine:
- Enhancing Design and Development
- Optimizing Operational Efficiency
- Improving Safety and Risk Management
- Ensuring Regulatory Compliance
Let’s break these down.
Enhancing Design and Development
Simulation plays a crucial role in speeding up the design process by allowing engineers to analyze performance under various conditions (Figure 2). This replaces costly and time-consuming traditional testing with fast virtual iterations. The result is safer and more efficient designs that reach the market faster and at a lower cost.
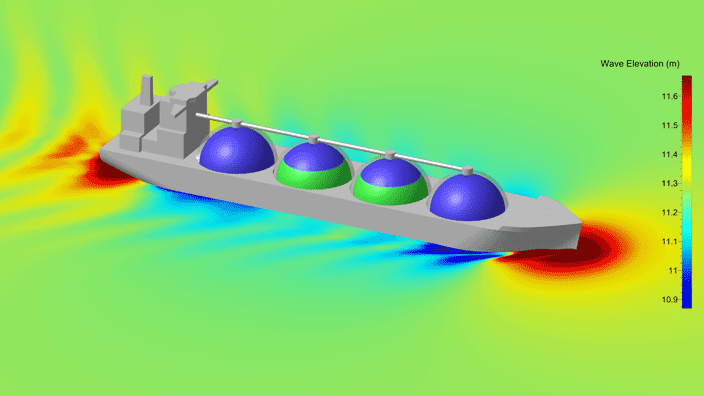
Optimizing Operational Efficiency
Efficiency is key in the marine industry, where fuel costs and downtime heavily impact profitability. Marine simulations help optimize:
- Vessel speed and cargo load for better fuel efficiency.
- Predictive maintenance schedules to reduce unplanned breakdowns and improve fleet reliability.
Improving Safety and Risk Management
Safety is non-negotiable in the maritime sector. Accidents and equipment failures can have devastating consequences. Simulation helps by:
- Identifying risks in the design and operation stages.
- Training crew with realistic emergency scenarios, improving preparedness and response.
Ensuring Regulatory Compliance
The marine industry faces strict regulations around safety, emissions, and environmental impact. Simulation enables companies to:
- Pre-test vessels for compliance with regulatory standards.
- Minimize the risk of penalties and reputational damage. This is especially critical in today’s push for sustainable, low-emission operations.
Incorporating Fidelity Fine Marine into your strategy ensures that your designs are innovative, compliant, and optimized for performance—setting you up for long-term success.
Implementation of Marine Simulation Projects
Implementing marine simulation projects requires a structured approach to ensure that outcomes meet design, performance, and business expectations. Here’s a step-by-step breakdown of the process.
1. Project Definition and Scope
Every successful project begins with clear objectives.
- Define the goal: Improving hydrodynamic efficiency, enhancing safety, or optimizing operational performance.
- Determine the project scope: Identify the marine environment elements to include, such as wave dynamics, weather conditions, or interactions with other vessels and structures.
2. Data Collection and Preparation
Accurate data is crucial for reliable simulation results.
- Collect data on hydrodynamics, structural configurations, material properties, and environmental conditions.
- Validate the data through cross-referencing with historical data or conducting preliminary tests to ensure relevance and accuracy.
3. Tool Selection and Setup
Choose the right simulation software based on:
- Analysis requirements
- Complexity of the simulation
- Factors such as accuracy, automation, AI integration, and high-performance computing (HPC).
After selection, configure the software and integrate it with the existing IT infrastructure for seamless data flow and processing.
4. Computational Model Development
Model development is a technical process that involves several key steps:
- Geometric modeling: Create a detailed representation of the vessel and environment using CAD software.
- Meshing: Divide the geometry into discrete elements for computational analysis.
- Set initial and boundary conditions: Define the starting state and the simulation domain’s limits.
- Select mathematical models: Choose models for laminar or turbulent flows to represent real-world physical phenomena accurately.
5. Analysis and Optimization
This phase involves solving the computational models to understand vessel performance.
- Monitor simulations to ensure relevant outputs and make adjustments as needed.
- Analyze results to assess stability, resistance, propulsion efficiency, and safety margins.
- Validate by comparing results with experimental data or theoretical predictions.
Once validated, the next step is optimization:
- Refine the hull design, adjust weight distribution, or modify operational protocols.
- Iterative simulations help reach the optimal design and performance setup.
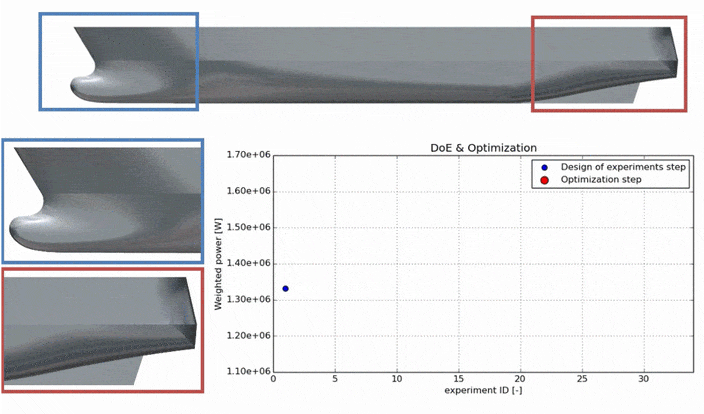
6. Final Steps
In the final phase, the optimized designs are implemented in vessel production or operational protocols. Key tasks include:
- Real-world testing to verify that changes deliver expected improvements.
- Documentation: Record every aspect of the simulation process—setup, adjustments, and outcomes—for future reference.
- Prepare reports and presentations to communicate findings to stakeholders for informed decision-making.
In the post-project review, conduct a comprehensive review to assess what worked well and what can be improved.
- This evaluation ensures continuous improvement and builds on the lessons learned to enhance future projects.
By following this structured approach, marine simulation projects can deliver tangible improvements in design, performance, and efficiency while minimizing risks and ensuring compliance.
Overcoming Marine Engineering Challenges
Adopting simulation-based design in marine engineering brings significant advantages but also introduces unique challenges. Here’s how simulation tools like Fidelity Fine Marine help address and overcome these obstacles.
Complexity of Setup and Use
Advanced simulation software can be intimidating for teams without specialized knowledge. Fidelity Fine Marine simplifies this process with:
- Customized Graphical User Interface (GUI) for intuitive navigation.
- C-Wizard Tool (Figure 4): This automation tool streamlines simulation setup by configuring parameters such as speed, angle, sea conditions, and geometrical variations, significantly reducing engineering time and making the software more accessible to non-specialist users.
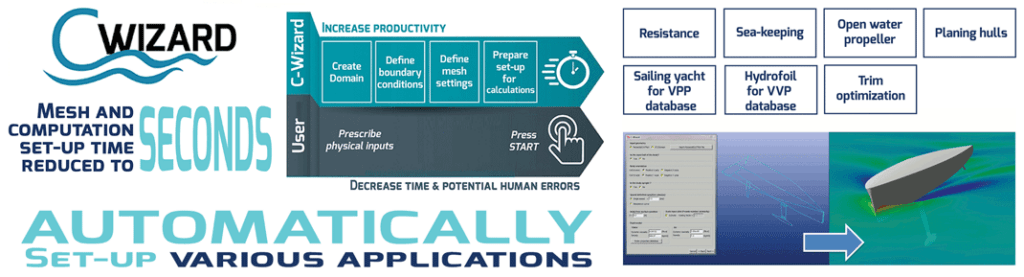
High Cost of Experimental Facilities
Traditional methods like towing tanks and wind tunnels are expensive and require scale models, which may not always represent full-scale scenarios accurately. Fidelity Fine Marine acts as a virtual towing tank and wind tunnel, allowing for full-scale simulations, eliminating the need for costly physical models, and improving accuracy and reliability.
Accurate Representation of Complex Fluid Interactions
Simulating complex fluid interactions, including free surfaces, turbulence, and air-water interfaces, is technically demanding. Fidelity Fine Marine addresses these challenges with advanced features such as:
- Efficient free surface modeling for wave interaction.
- Advanced turbulence models for accurate flow representation.
- Adaptive grid refinement, ensuring high-resolution simulations for mono- and multi-fluid flows around any marine vessel (Figure 5).
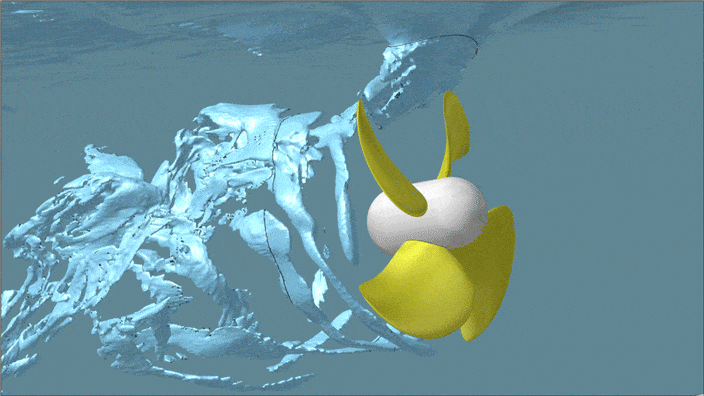
Achieving Regulatory Compliance
Navigating stringent international regulations, such as the Energy Efficiency Design Index (EEDI) and Energy Efficiency Existing Ship Index (EEXI), can be complex. Fidelity Fine Marine helps ensure compliance by calculating energy efficiency and CO2 emissions during the design phase, well before physical trials. This proactive approach allows engineers to optimize ship designs for maximum efficiency and meet international standards with confidence.
By leveraging Fidelity Fine Marine, engineering teams can overcome these challenges effectively and unlock the full potential of simulation technology.
Real-World Applications of Marine Simulation
Simulation plays a crucial role in modern maritime design and operations, offering insights that drive innovation and support strategic decisions. One notable example is hull shape optimization for improving fuel efficiency in passenger ferries, highlighting how CFD simulation can make vessels more sustainable while reducing operational costs.
With the introduction of the International Maritime Organization (IMO2023) regulations, the maritime industry has been under increasing pressure to reduce carbon emissions:
- 40% reduction by 2030
- 70% reduction by 2050 (compared to 2008 levels)
To meet these stringent targets, a large passenger ferry company turned to CFD to optimize hull designs and improve fuel efficiency.
Using Cadence Fidelity CFD, the company embarked on a project to reduce the power required to maintain various cruise speeds under different loading conditions. The goal was to minimize fuel consumption while maintaining performance across all operational scenarios (Figure 6).
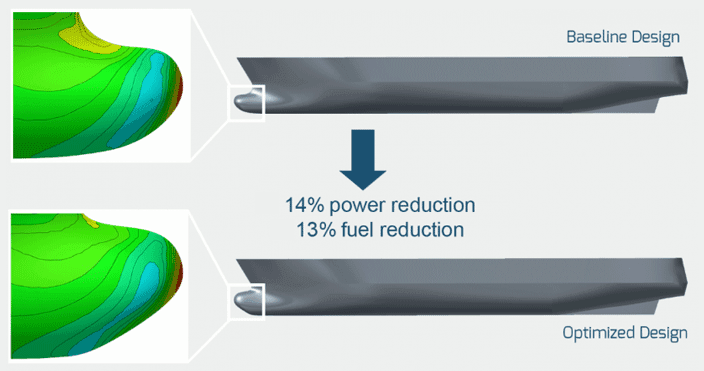
Key Steps in the Optimization Process:
- Parametric Hull Modeling: The engineers created a parametric model directly integrated into Fidelity Fine Design3D for fully automated design optimization.
- C-Wizard Automation: This tool simplified the setup, focusing on weighted power reduction, streamlining the analysis process, and skipping preliminary tests to move straight into optimization.
- Self-Propulsion Simulations: An enriched actuator disk model was used to simulate the propeller’s influence on performance, providing critical insights into fuel consumption under real-world conditions.
The results of this comprehensive optimization were impressive. Under typical operational conditions, the optimized hull design achieved:
- Average power reduction: 14.08%
- Fuel consumption reduction: 13.53%
This translated into substantial financial savings—the company projected an annual fuel cost reduction of $337,000 per vessel (for two engines). Beyond financial benefits, the optimized design significantly reduced carbon emissions, aligning with the company’s sustainability goals and ensuring compliance with IMO regulations.
Conclusion
Simulation is reshaping the marine industry, offering new possibilities in design, operations, and safety that were once beyond reach. For managers and engineers alike, adopting a simulation-based approach is no longer just an option—it’s a strategic necessity in today’s fast-evolving maritime landscape. Fidelity Fine Marine equips organizations with the ability to stay ahead of industry demands, reduce costs, and meet growing regulatory pressures, all while optimizing performance and safety across marine operations.