Key takeaways from this article:
- Understand the basics of aeroacoustics and the strategic importance of aeroacoustic simulation.
- An overview of the main challenges facing managers in general – and how to overcome these managerial challenges.
- Cost-benefit analysis of aeroacoustic simulation.
- A practical examples of CharLES (aeroacoustic simulation) used in action.
Aeroacoustics delves into the noise generated by air movement, particularly in and around objects. It’s about understanding how fluid dynamics, such as air, produce sound, particularly when interacting with various surfaces. However, for businesses and managers, having a foundational understanding of aeroacoustics is crucial for informed decision-making.
Contrary to popular belief, aeroacoustics is not a new field. Ever since humans took to the skies or designed high-speed trains, the challenge has been not only to make them move fast but also to mitigate the noise they generate.
The primary goal in aeroacoustics is to anticipate, quantify, and manage noise. Although it is grounded in mathematics, physics, and computational modeling, the practical applications are what’s truly captivating. From designing quieter aircraft engines (See Figure 1 below) and wind turbines to optimizing airflow around structures to mitigate urban noise, aeroacoustics has a wide range of practical applications.
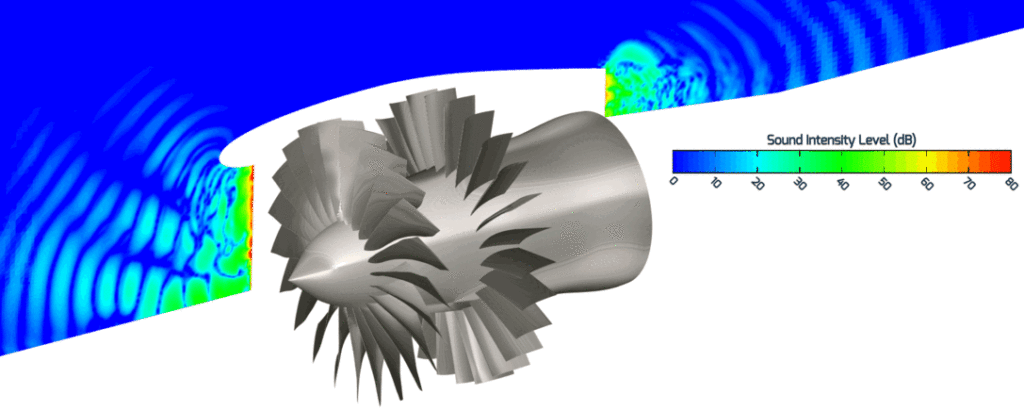
If you’re interested in delving into the technicalities or aiming to bridge the gap between management and engineering, gaining a deeper understanding of the subject can prove to be beneficial for you.
We’ve made a corresponding guide for engineers: Simulating Aeroacoustics: An Engineer’s Guide. This guide explores the nitty-gritty of aeroacoustic simulations, ranging from fundamental principles to advanced techniques. Whether your goal is to enhance dialogue with technical teams or simply improve your expertise, this guide is a great place to start.
How noise can impact your business and the strategic importance of aeroacoustic simulation
Noise isn’t merely a matter of environmental or auditory concern; it’s a significant business consideration. Across various industries, noise can impact customer satisfaction, product usability, and ultimately, sales. Take, for example, the appeal of a quieter airplane cabin, which can greatly enhance the overall flight experience and serve as a competitive advantage for commercial airlines. In addition, aircraft manufacturers face ongoing regulatory pressure to minimize noise levels around airports, impacting routes, schedules, and profitability.
And, in a world increasingly focused on sustainability and quality of life, noise pollution is getting more attention from both the public and regulatory bodies. Consumers and regulators are pushing companies to reduce their acoustic footprint, directly affecting branding, public relations, and market positioning. Not to mention, non-compliance with noise regulations can result in substantial penalties and legal consequences.
Expertise in aeroacoustics isn’t just a technical necessity; it’s a strategic imperative. Businesses well-versed in this field will be better equipped to tackle the challenges and capitalize on the opportunities presented by sound — or the absence thereof— in today’s market landscape.
Aeroacoustic simulations carve out a unique niche within the vast world of simulations and modeling. While engineers and experts handle the technical aspects, from a strategic standpoint, these simulations provide distinctive advantages capable of influencing business trajectories. Here’s how.
Enhancing Product Design and Efficiency
In today’s consumer-driven market, achieving excellence in product design is a constant pursuit. Aeroacoustic simulations provide crucial insights that can significantly impact the design process. For example, take the automotive industry; a car’s acoustic profile, including wind noise at high speeds to the cabin’s insulation capabilities from outside sounds, can strongly influence consumer preferences. By simulating aeroacoustics, manufacturers can refine designs to ensure a harmonious balance between aesthetics, functionality, and acoustic comfort.
Meeting regulatory standards
Noise emission regulations, especially in aviation and renewable energy sectors, grow more stringent by the day. For example, the European Union Aviation Safety Agency recently introduced the Environmental Protection Technical Specifications, establishing noise certification standards for electric vertical take-off and landing (eVTOL) aircraft (Refer to Figure 2). Failing to meet such standards can result in significant penalties, operational constraints, or product recalls. Aeroacoustic simulations enable businesses to anticipate and address regulatory requirements proactively, ensuring compliance before products enter the market. This proactive approach not only mitigates potential penalties but also expedites the certification process, reducing time-to-market.
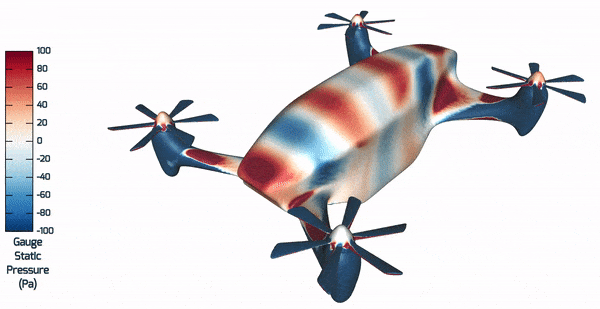
Securing a competitive advantage
Today, setting yourself apart from the competition is key to stand out in a crowded marketplace. Aeroacoustic simulations can give you that advantage. Whether it’s a quieter aircraft, a less noisy wind turbine, or a noise-free vehicle, such innovations appeal to consumers who prioritize tranquility. Additionally, demonstrating a commitment to noise reduction can significantly enhance a brand’s image, signaling environmental responsibility and customer care.
However, the benefits extend beyond immediate gains, there’s a key advantage to leveraging aeroacoustic simulations: future readiness. As urbanization accelerates and sustainability becomes increasingly important globally, effective noise management will be essential.
In summary, aeroacoustic simulations aren’t just about decibels and airflow; they represent strategic assets that shape product evolution, inform business strategies, and pave the way for market leadership.
Main challenges of aeroacoustics facing managers
Aeroacoustic projects pose unique challenges for managers. They go beyond the regular hurdles faced in typical projects, and they demand a nuanced understanding, effective communication, and adaptable strategies. Here, we outline the key hurdles managers face in simulating aeroacoustics and offer insights into effectively managing them.
- Bridging Technical and Strategic Realms: One of the main challenges is seamlessly integrating technical expertise with strategic objectives. As a manager, your job is to ensure that the technical efforts align with the project’s primary goals. It demands a comprehensive understanding (both technical and strategic) as well as clear and effective communication.
- Resource Allocation and Budgeting: Balancing the need for specialized resources with budget constraints is a delicate balancing act. High-end computational resources, specialized software, and niche expertise are often needed in projects involving aeroacoustics.
- Staying up to date with technological advances: Due to the ever-evolving space of aeroacoustics, you need to make sure your team has access to the latest tools and knowledge, which also, requires you to stay in the loop on industry advancements.
- Managing expectations: Stakeholders, both internally (higher management, investors, etc.) and externally (clients, consumers, regulatory bodies, etc.) might have specific expectations. Juggling these expectations can be very challenging, especially, because they might not always align with technical realities.
- Risk management: Anticipating and mitigating potential uncertainties inherent in aeroacoustics simulations is crucial. From potential software glitches to misjudged simulation parameters, risks abound. As a manager, you need to have a steady hand when assessing risks and implementing mitigation strategies.
- Nurturing effective collaboration: Orchestrating seamless collaboration among diverse teams, from acoustic experts to software engineers, is essential for your project’s success. But it’s not easy, it requires a lot of structure and transparency to ensure that these teams can collaborate effectively, communicate seamlessly, and work towards a unified goal.
- Navigating regulatory and compliance challenges: Here, there’s no place for compromising. You need to guarantee that your aeroacoustic projects live up to industry standards, regulations, and compliance norms. Failing to do so can be fatal.
While these challenges may seem daunting, with the right approach and resources, you can transform them into opportunities for growth, innovation, and accomplishment.
Overcoming managerial challenges
We just outlined the challenges of simulating aeroacoustics from a manager’s perspective. But, in our world, if there’s a problem there’s a solution. So, let’s look at a potential solution for today’s managers. Let’s talk about Fidelity CharLES, a contemporary tool with technological advancements paving the way for more cost-effective, efficient, and accurate simulations.
Fidelity CharLES
Fidelity CharLES stands out among computational fluid dynamics (CFD) solvers, designed to empower design engineers with high-resolution simulations at their fingertips. Offering unparalleled speed and accessibility, CharLES is optimized for both graphics and central processing units, ensuring seamless performance. Its versatility extends to various applications, including jet engine combustors and vehicle external aerodynamics.
Picture this, a tool finely tuned for the flow conditions typical in aeroacoustic simulations, equipped with algorithms capable of precisely handling complex scenarios. CharLES excels in solving aeroacoustic problems with a high accuracy and stability, thanks to advanced numerical methods tailored for sound analysis.
Moreover, CharLES features a user-friendly interface that balances sophistication and practicality, catering to seasoned experts and newcomers. Its intuitive design promises a smooth workflow from setup to execution, making it particularly beneficial for users exploring CFD without extensive background knowledge. Additionally, CharLES offers a high degree of customizability, allowing users to tailor simulations to their specific requirements.
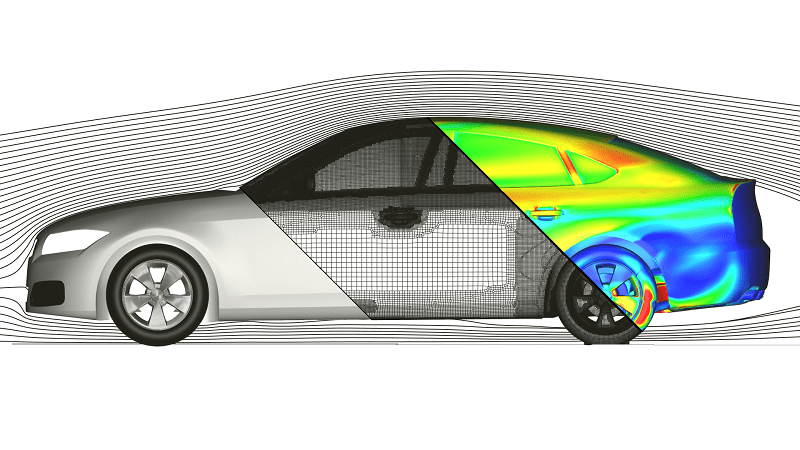
So, what makes CharLES stand out from the alternatives?
it’s all about the capability to anticipate and tackle intricate CFD obstacles accurately, quickly, and economically. These include aeroacoustic noise, turbulent mixing, flow separation, transition, turbulent shear stress, and heat transfer, alongside combustion and emissions.
Anticipation
CharLES’s solver stands out thanks to its use of large-eddy simulations (LES), providing an unprecedented level of precision and reliability rare to many commercial CFD tools. Grounded in fundamental physics principles, its LES model ensures stability and accuracy, resulting in unparalleled accuracy in capturing complex flow phenomena.
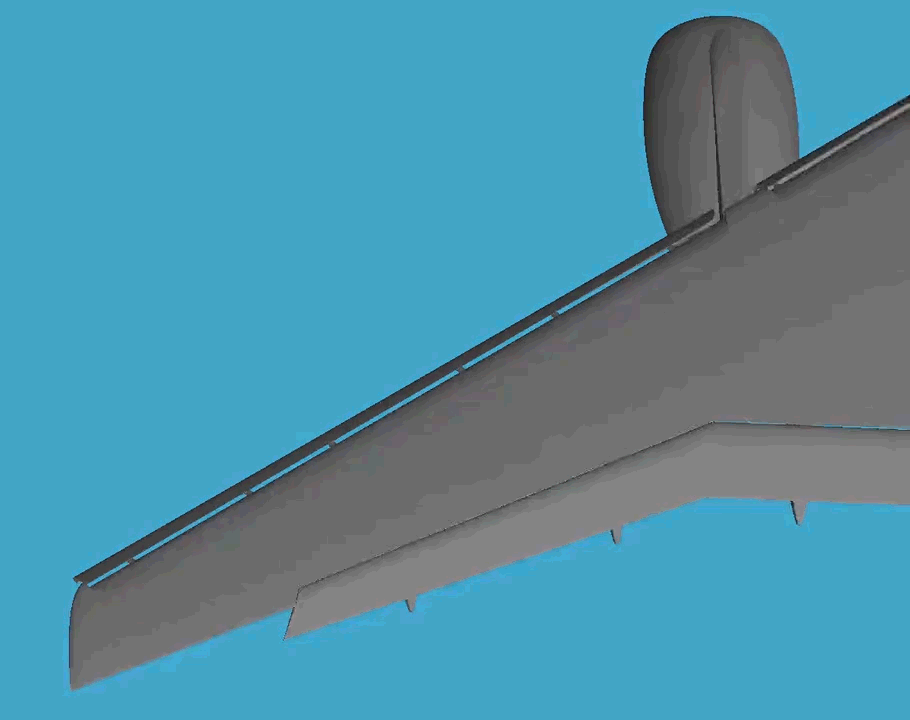
Simulation speed
In today’s fast-paced design environment, speed is paramount. CharLES’s solvers are designed for extensive parallel processing and scalability, maximizing computational resources to deliver timely results. With advanced load-balancing algorithms, CharLES intelligently allocates the computational load across processors or computing nodes, minimizing idle time, and maximizing efficiency.
Moreover, CharLES optimizes memory usage to eliminate excessive memory allocation, crucial for large-scale simulations where memory can be a bottleneck. Its adaptable architecture ensures scalability across platforms and operating systems, whether on a local workstation, high-performance computing cluster, or cloud-based infrastructure. Real-time monitoring features provide insight into computational performance, empowering users to optimize efficiency during long-running simulations.
Cost-efficiency
While historically optimized for CPU-based clusters, CharLES’s solvers excel in accelerated node architectures dominating top-tier supercomputing platforms. By harnessing GPU architectures, CharLES significantly reduces computational time compared to traditional CPU setups. This efficiency translates to potential cost and energy savings, making it a game-changer for large-scale simulations requiring swift turnaround times.
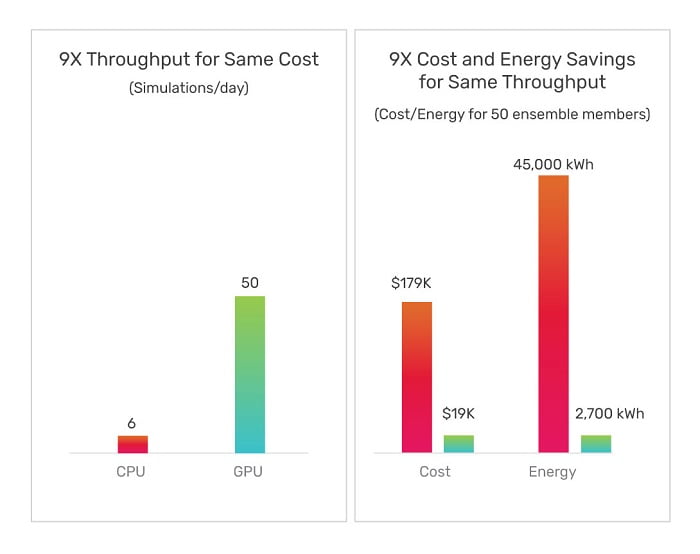
Take that in, 9x throughput for the same cost of CPU and 9x lower cost and 17x less energy for the same CPU throughput.
Go watch the NVIDIA Keynote Address.
Cost-Benefit analysis
Naturally, it’s important to understand the associated costs and potential returns before diving into any strategic decisions, especially one involving adopting new technologies like aeroacoustic simulations.
The upfront costs
Let’s be honest, of course, integrating aeroacoustic simulations does with its set of costs. As mentioned, High-fidelity simulations demand robust computational infrastructure, including powerful servers and specialized software. Additionally, having the right human resources — e.g. experts in aeroacoustics — is vital, which may necessitate hiring new talent or training existing staff. Moreover, specialized software for aeroacoustic simulations often entails significant licensing fees.
The hidden savings
However, while the initial costs may seem daunting, the long-term savings can outweigh them. Accurate simulations can reduce the need for multiple physical prototypes, leading to substantial savings in materials, labor, and time. Proactively addressing noise concerns can also prevent costly regulatory fines and potential litigations. Testing at full scale in an anechoic chamber is both cumbersome and expensive, but virtual testing eliminates the need for physical redesigns.
The long-term benefits
Beyond immediate savings, aeroacoustic simulations can provide intangible benefits that significantly impact the bottom line. Establishing a reputation as an industry leader in noise management can enhance brand reputation and influence customer purchasing decisions. Moreover, products compliant with global noise standards can access a broader range of markets without regulatory hurdles. Additionally, insights from simulations can inspire innovative product features or entirely new product lines, creating opportunities for revenue generation.
Weighing the pros and cons
Ultimately, the decision to integrate aeroacoustic simulations hinges on whether the strategic advantages and long-term benefits outweigh the initial investments. For many businesses, particularly those in sectors where noise management is critical, the answer is a resounding “yes.”
As a manager, understanding this cost-benefit interplay enables you to make informed decisions, aligning technical investments with key business objectives and fostering sustainable growth in a dynamic market landscape.
CharLES in action
Aeroacoustic simulations hold significant industrial relevance, spanning from supersonic aircraft noises to fan sounds. Table 1 outlines several noteworthy applications where CharLES has demonstrated its effectiveness, including VTOL rotor and sedan noise predictions with Honda R&D, as well as NASA’s fan noise source diagnostic test (SDT).
SDT (low noise OGV) | Full-Scale Sedan | Multibladed Rotors | |
Grid Resolution (million control volumes) | 142 | 118 | 30 (multibladed rotor); 137 (full-scale eVTOL aircraft) |
GPU Run-Time | ≈6 hours on 40 Nvidia V100 PCIe GPUs | ≈1.5 hours on 32 Nvidia V100 GPUs | <12 hours on 40 AMD Mi210 GPUs (full-scale eVTOL aircraft) |
CPU Run-Time | ≈24 hours on 4096 AMD 7H12 Rome CPUs | ≈6 hours on 2560 AMD EPYC CPUs | 36 hours on 2016 SGI ICE XA Intel Xeon E5 2697 v4 CPUs (full-scale eVTOL aircraft) |
Relative Error (Overall Sound Pressure Level) | 1.12% | Within ± 5 dB of experimental values | <2% for all multibladed rotors |
Investigation of VTOL Rotor Noise with Honda R&D
Researchers conducted a study on multi-bladed VTOL rotors, commonly found in modern drones and urban vehicles, to assess the accuracy and cost-effectiveness of high-frequency aeroacoustic simulations. They examined various rotor configurations, ranging from two to five blades, and compared the results with data obtained from Honda’s wind tunnel tests.
The analysis revealed a noticeable increase in noise levels with the addition of rotor blades, aligning with experimental findings. Additionally, CharLES was utilized to simulate a full-scale eVTOL aircraft featuring eight VTOL rotors and a pair of propellers, showcasing the software’s extensive capabilities and efficiency, particularly when coupled with GPU acceleration.
Noise Predictions for a Full-Scale Car with Honda R&D
Honda R&D analyzed the sound profile of a sedan traveling at 120 kph, aiming to validate its predictions against real-world wind tunnel tests. Simulations were conducted with two different grid resolutions, with the refined version revealing intriguing airflow patterns, particularly around the A-pillar, which can impact the car’s performance and noise emissions. To ensure accuracy, simulation outcomes were compared to actual wind tunnel data, demonstrating close agreement between the two. Additionally, leveraging specialized graphics hardware (GPUs) significantly accelerated the simulations compared to traditional computer processors (CPUs).
NASA’s Fan Noise Source Diagnostic Test
In collaboration with NASA, CharLES conducted a fan noise Source Diagnostic Test (SDT), to assess the impact of various outlet guide vane (OGV) designs on fan aerodynamics and noise levels. The comprehensive computational setup encompassed the entire test section, nacelle, and the full annulus of the fan and OGVs, simulated at 61.7% of its normal speed. Subsequently, it was discovered that the low noise OGV design reduced noise levels by approximately 2 dB—a significant improvement, with simulation results aligning closely with experimental data. Impressively, CharLES exhibited remarkable accuracy even with a relatively coarse mesh.
CharLES consistently delivers high accuracy compared to real-world experiments. Leveraging GPU acceleration, the solver ensures rapid simulations without sacrificing detail. The software is accessible through conventional client site setups and dedicated cloud solutions, offering flexibility to meet diverse needs.
Summary
Simulating aeroacoustic phenomena requires more than technical expertise; it demands strategic oversight, robust collaboration, and decision-making. This guide aims to provide managers (like yourself) with a comprehensive understanding of aeroacoustics, emphasizing their crucial role in aligning technical intricacies with broader business objectives.
Throughout our exploration of essentials, from fundamentals to risk management, one theme remained constant: the importance of teamwork. Effective collaboration between managers and engineers is essential for driving projects towards success.
Aeroacoustic simulations, with their far-reaching implications across industries such as aerospace and automotive, are composed to shape the future. Equipped with the insights, tools, and strategies discussed in this guide, you’ll have the tools to lead the way.