It is not uncommon for CFD engineers to simplify complex shapes to make meshing easier. While this can save time, it often sacrifices the precision of their simulations, impacting performance.
Over the years, we've seen considerable efforts to develop algorithms that automate mesh generation, enhancing accuracy and reducing manual intervention. Take, for example, healthcare devices such as artificial tricuspid valves – the need for precision here is paramount, as human lives are at stake. Automated mesh generation can significantly cut down the time spent on repetitive tasks, a boon in such critical scenarios. Let's find out how.
Why is mesh generation so time-consuming?
CAD preparation (geometry and cad cleanup) is the most tedious and time consuming part of the CFD process, generally amounting to 80% of the total time spent on a CFD simulation.
When preparing for a CFD simulation, engineers face several pain points:
1. Geometry preservation
Maintaining the intricate features of complex geometries while meshing can be difficult due to the need for geometry precision. Ensuring that the mesh accurately reflects the geometry's intricacies often involve manual adjustments and refinements. Simplifications or approximations may lead to inaccuracies in the CFD simulations.
2. Mesh generation
Creating high-quality meshes for complex geometries requires careful consideration of cell size, shape, and connectivity. And manually creating these can be both time-consuming and incredibly tedious, especially for large geometries.
Engineers often spend a substantial amount of their time on mesh generation alone.
3. Mesh Quality and reliability
Generating meshes that accurately capture flow phenomena like separation, shear layers, and stagnation points requires well-structured and high-quality cells. Ensuring these qualities can be challenging due to the complex geometry's impact on mesh quality.
Engineers may need to spend additional time refining and optimizing the mesh to achieve the desired quality. Poor mesh quality can lead to inaccurate results and convergence issues.
4. Mesh adaptation and refinement
Determining where and how to refine the mesh to ensure accuracy in simulations, particularly in areas with complex flow patterns, can be challenging. This process involves identifying regions that require refinement based on solution errors.
The iterative nature of mesh adaptation and refinement, where the mesh is adjusted based on simulation results, can extend the simulation setup time.
5. Moving geometries
Simulating scenarios where the geometry changes over time, such as moving vehicles or rotating machinery, requires dynamic mesh generation solutions that adapt to these changes. Implementing such dynamic meshes can be technically challenging.
The benefits and limitations of manual vs. automated mesh generation speak for themselves:
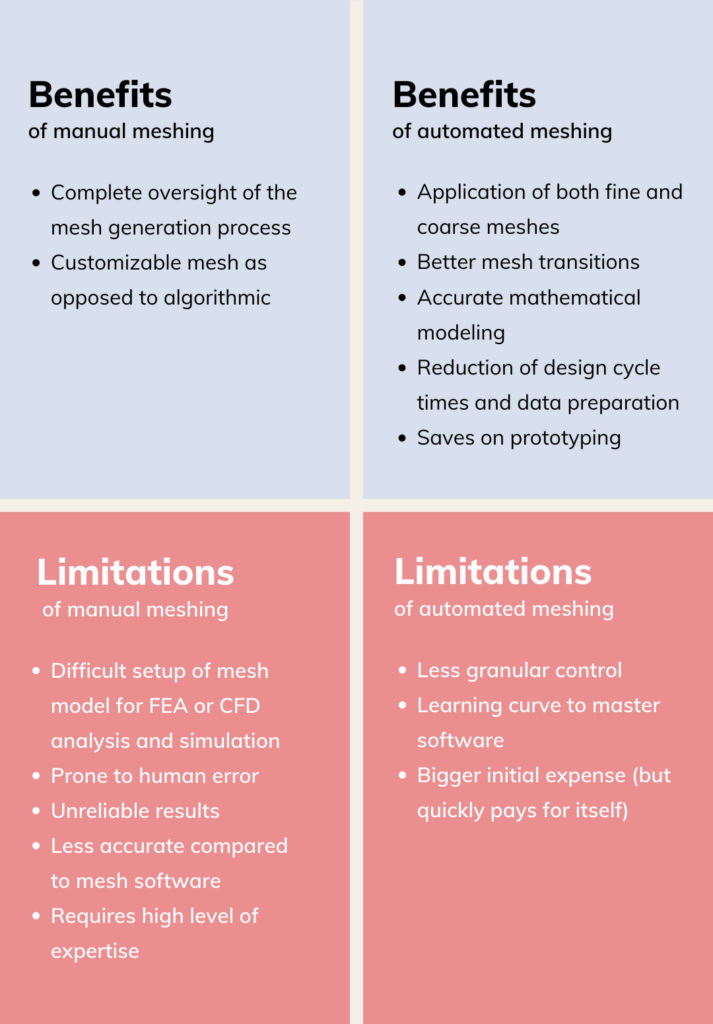
The obstacle course of mesh generation
Mesh generation is akin to crafting a precise blueprint for a complex structure, ensuring stability and accuracy. Yet, it's far from a straightforward task. Let's delve into five distinct mesh generation challenges that confront every CFD engineer. These hurdles demand careful consideration, but with the right strategies, they can be overcome - don't worry, we'll show you how.
Minimum user experience
Creating an impeccable mesh has traditionally been an art mastered over years. However, the prospect of software that respects design geometry and minimizes the learning curve offers the promise of enhanced efficiency and flexibility.
Structured and unstructured grids
The choice between structured and unstructured grids hinges on the complexity of the geometry at hand. While structured grids excel in efficiency, they often fall short when dealing with intricate shapes. Unstructured meshing steps in to address this challenge.
High-resolution mesh generation
Achieving excellence in fields like automotive design necessitates a meticulous approach. This involves refining the mesh in critical areas, including boundaries, walls, and off-body regions, to capture intricate flow physics.
Faster computation and high accuracy
Traditional mesh generation methods can falter in the face of high Reynolds numbers and complex eddies due to the sheer volume of cells required. High-order meshing, coupled with high-performance computing, presents a potential solution, albeit with cost considerations.
Accommodating moving mesh models
In applications like turbomachinery, where fluid domains evolve dynamically, maintaining solution quality is paramount. This requires the deployment of moving mesh algorithms to keep pace with fluid dynamics.
Implementing automated meshing successfully with Pointwise
Now, having a visual projection of how your geometry is going to be meshed and discretized, before running any sort of mesh generation tool, is very helpful. This allows you to verify all the inputs of your meshing setup without having to run anything. And in some regions, a high level of detail is going to have critical impact on your CFD simulation and its reliability.
Because at the end of the day, you want to make sure that what’s on your screen corresponds as much as possible to what’s going to be ending up in your wind tunnel or in your test track.
One of the most efficient ways to cut down on time and to maintain the highest level of accuracy and reliability in your results is to have it all under control within the same environment with the possibility to make it fully automatic. This way, you can seamlessly integrate it into your existing workflow according to your needs.
With Pointwise, no compromises are made. Our track record so far is reducing pre-processing time from more than three weeks to 1-2 days.
As you can see, Pointwise offers a suite of built-in tools designed to simplify the grid discretization workflow for complex geometries.
Let's explore some of its key offerings:
1. Flashpoint: Automated Surface Meshing Tool: With minimal input required, Flashpoint automatically generates surface meshes. This tool is especially handy when you need to capture complex geometry curvature, like the leading edge of an aircraft wing.
2. T-Rex: Anisotropic Near-body Meshing Tool: T-Rex specializes in near-body or boundary layer meshing. It excels at handling symmetry boundaries, sharp edges, and thin surfaces. It generates layers of prisms and hexahedra to resolve near-wall flows and automatically adjusts extruding layers to avoid collisions.
3. Voxels: Automated Off-Body Surface Meshing: Voxels offer high-quality, uniform cells for off-body meshing. This tool removes voxels intersecting with geometry and excels in both internal and external flow geometry.
4. Mesh Adaption: Automated Tool for Refinement: Mesh Adaption refines meshes where needed based on flow solution error estimates. It's great for achieving uniform and high-resolution meshing, especially in off-body regions.
5. High-Order Curved Meshing: This advanced technology leverages High-Performance Computing (HPC) to generate meshes with fewer elements, high accuracy, and reduced memory usage. It's a game-changer for challenging scenarios like high Reynolds numbers.
6. Overset Meshing: Suitable for moving body applications, overset meshing recomputes mesh connectivity for changing fluid backgrounds. This method shines in turbomachinery, capturing moving body physics efficiently.
Let's sum up
Accurate meshing is crucial, as it impacts numerous applications with real-world implications. Cadence Pointwise's diverse meshing technologies make it suitable for a wide range of domains, from turbomachinery to medical applications. It offers a flexible solution for automating complex grid discretization workflows without compromising accuracy.
With automated meshing, you:
- streamline the mesh generation process, significantly reducing the time required to create meshes.
- accurately capture complex geometry details, thus ensuring that critical features, such as leading edges or intricate shapes, are preserved, resulting in more accurate simulations.
- ensure that cells are well-shaped and free from issues like skewness or distortion, leading to more reliable CFD results and smoother convergence.
- reduce the learning curve for mesh generation, allowing your team to onboard new talent more quickly.
- automatically identify regions that need refinement based on solution errors, ensuring that computational resources are used efficiently.
- reduce the need to repeat the same meshing processes for similar cases by creating templates or scripts to automate these tasks, saving time and reducing the risk of errors.